(Part 5 of 13 in series, Scaf 101)
This first build is the most obvious thing to assemble and you can do a lot with it. (Yes, it is not actually a cube; I suppose it’s a right cubic rectangle.) I’m going to give a TON of detailed instruction on this build with a million photos. On subsequent builds I’ll be brief.
Advanced: As I’m assuming this is the first build you have ever done, I’m keeping the diagonals to only two. However, if you bought the four extra 45° single outlets, you can add two 1-foot diagonal braces to the mid-sized sides. I’ll mention how to do this as we go along.
Prep
Begin by clamping the four 3-foot pieces into the elbows. Note that the threaded ends go in the elbows.
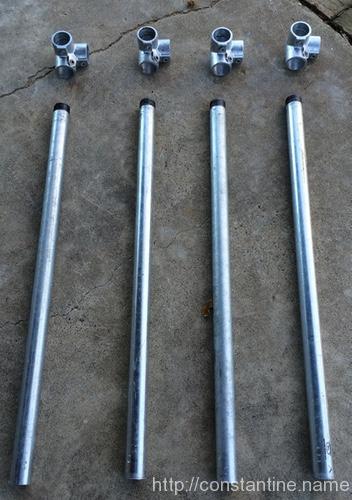
Notice the orientation of the clamps. The two set screws that will be used later, are facing the pipe. You’ll be happy these screws are facing up a few steps from now.
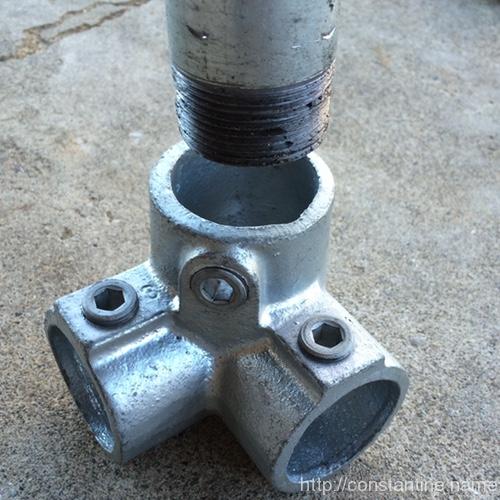
Why are we putting the threaded ends in these clamps? You’ll see why when we clamp the other ends of these pipes. For now, recall the discussions about inserting the pipes a little farther so the body of the pipe – i.e., not the tapered threads – is touching the inward land in the clamp.
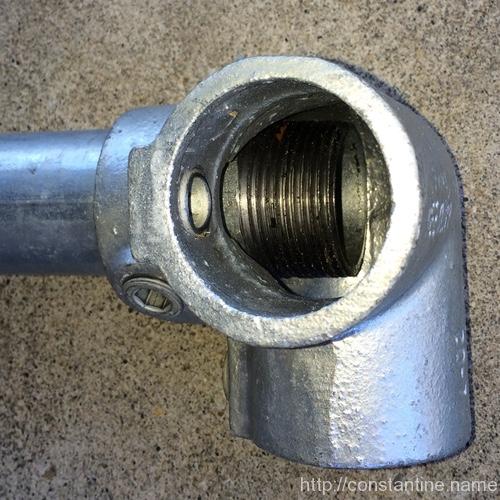
The bottom
Introducing the “layout” shot. I find it really helpful to lay everything out (until you get really good at scaf) so you can see that you have all the pieces you need. This is just a partial layout; it’s obviously not all the scaf for this build. In later builds, I’ll take an entire layout shot so you can see the mess. I think the layout (looking at a photo before it’s built) helps you visualize how you convert the loose junk into the finished product. Anyway, here’s the layout shot for the first corner:
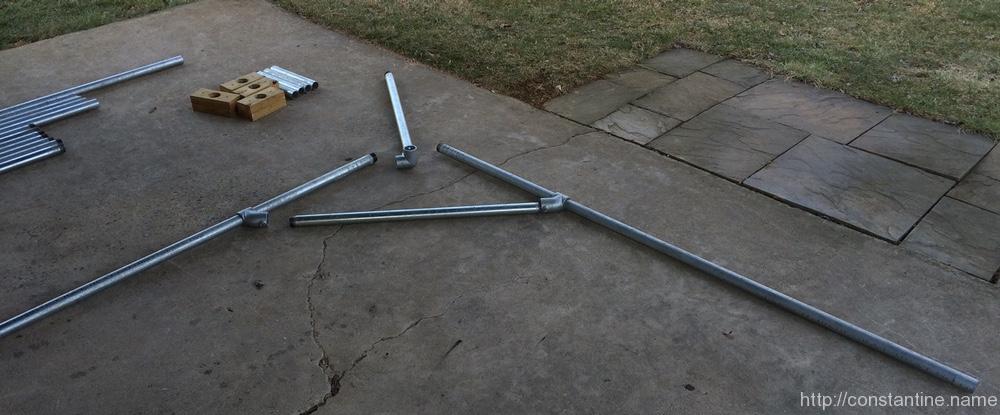
Of particular interest in the above shot: I’ve slid the two 45° single outlet tees onto the side pipes. That’s a 7-foot pipe on the right, a 5-foot pipe on the left, and the cross brace is another 3-foot pipe.
Below is, basically, another layout shot. Notice that I’m putting the threaded ends of the side pipes into this clamp. Can you guess why?
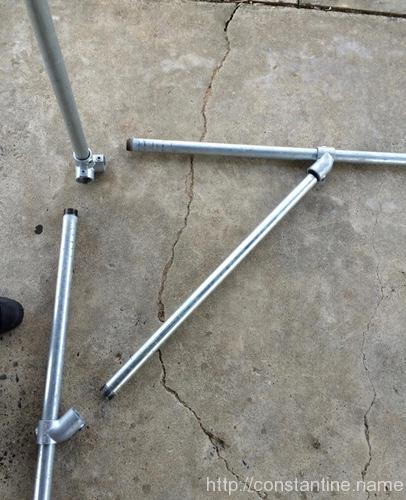
This is a hair splitting detail to deal with the fact that this pipe has threaded ends. This clamp already has the first pipe pushed a bit into the center space. So the next two pipes are not going to be able to be inserted extra to get their non-threaded bodies to the lands. (Boo!) But this problem has to happen somewhere in the build, right? So I’m doing this here, where there is a corner brace that will beef up this corner. Because all the pipes have one threaded end, this “fixes” two of the twelve threaded-end problems in this build.
Advanced: Turns out we’ll have both ends of the 3-foot pipes occupying the clamp bodies. So all of the 5-foot and 7-foot pipes’ threaded ends aren’t going to land perfectly. (Because, taper.) So, if you have the extra 45° single outlet tees, you can add a brace on each of the 3’x7′ sides. That will brace two more (one per each brace) of the remaining four threaded ends. Again, I’ll explain more as we go along.
Next is a finished shot of this corner assembly. Here you’ll see another reason why I love those wooden feet. Things like this are so much easier to assemble with the feet doing a little propping up. Note that this prop trick doesn’t always work. It’s handy here for this brace, but after this, the setup has to stay flat on the ground. We’ll do another angle brace soon, and it will be on the top face, so no need to prop it up.
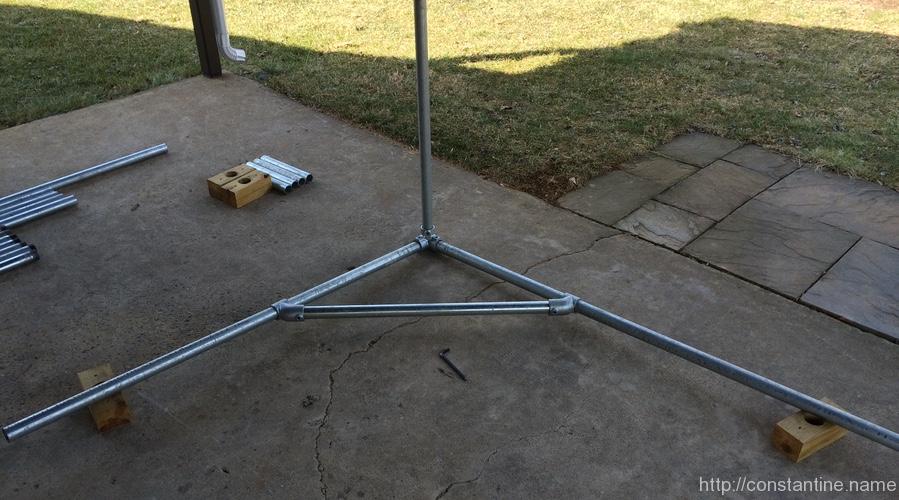
The next photo is the layout shot for the rest of the parts for this “lower” part of the cube.
Please notice that the next few photos incorrectly have the vertical 3-foot pipes with the threads out. Right after I took these photos, I realized it would be better with the threads in – which is how it’s described above, to this point. So I flipped the pipes around… and promptly forgot to retake these photos. When I realized these shots were wrong, I didn’t feel like doing the entire build all over… because this space is already full of other scaf. :^P
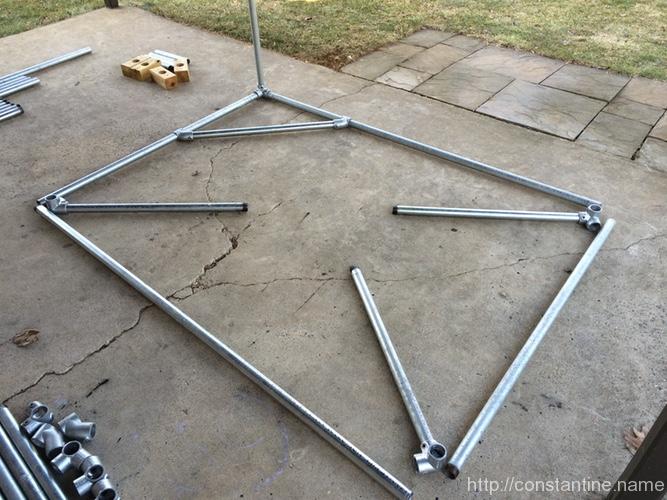
Advanced: If you have the extra 45° clamps, and want to add a brace, you should add a clamp where I have the red arrow. That’s the end of the 7-foot pipe that has a thread, and would most benefit from bracing. The clamp should angle towards the corner, since you’ll put the other clamp for this brace on the 3-foot, vertical pole. I’m splitting hairs here about where to put braces. But, this is meant to be educational, ‘ya know?
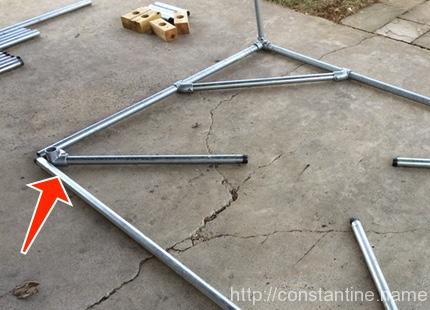
The next photo shows two more verticals, and the 7-foot side clamped tight. Just the fourth vertical, and the last, 5-foot side remain to be installed.
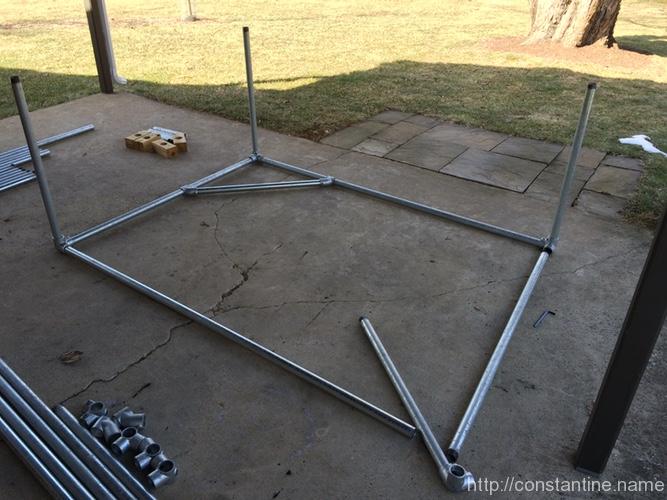
At this point, insert the 5-foot pipe into the clamp (the one towards the top of the photo.) The pipe, of course, will just lay there when you let go. Then clamp the fourth vertical to the pipe. (That’s the clamp/set-screw where the Allen wrench is laying.) You’ll have enough swing/wiggle in the 5-foot for this to be easy even with one hand always on the vertical pipe.
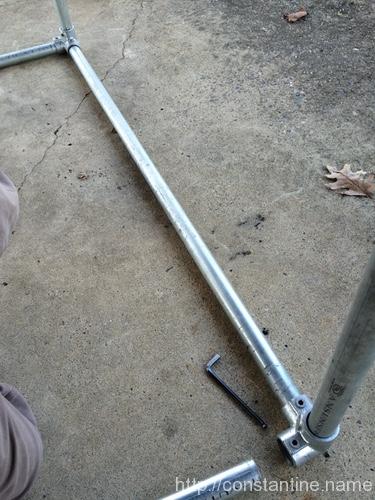
Why? Diatribe about safety: Yes, this build is pretty harmless. But as you build bigger things, you will live longer if you are always thinking, “when I forget and let go” or “when I slip” or “when I get stung by a bee and drop this part”. At this instant in the build, that fourth vertical looks like it’s attached – it’s clamped to the 5-foot side pipe, but the pipe is free to rotate but you cannot tell at a glance. The vertical may even stand for a while before falling over. This is exactly how someone gets hurt. Something that looks stable, actually isn’t clamped yet.
Now tighten the other screw on the vertical pipe’s corner clamp which fixes the 7-foot pipe into this corner.
Anything else? Yeup, the other end of that 5-foot pipe. Learn to keep track of what’s tight. Learn to spot proud set screws that need to be tightened (or whose clamp alignment needs fixing so the screw goes in farther). While you’re at it, give the structure a couple shakes, and then go check every set screw.
Pro-tip: Soon you will have a feel for “this is how much I torque these things” and you’ll go around and just sort of torque torque torque them quickly. In an instant, you can apply “just that right amount of torque”, and when the screw doesn’t move, you’re happy. This is another way to spot good scaf builders: They do not go around and actually tighten each screw a little bit more each time. (The screws cut hickies the tighter you make them.) Good scaffers know what a tight set screw feels like before it moves.
Mastery-tip: The set screws scratch the steel pipes and move the Zinc coating. That leads to a tiny bit of corrosion between the pipe and the screw, which makes the set screw stick in place. That’s a good thing because it helps prevent things wiggling loose. So if you’re in the habit of actually moving each screw when you periodically check things, then you’re messing up the one time when corrosion is actually working in your favor.
So, here’s what you have, everything tight and ready for the upper frame (except, of course, your 3-foot verticals are not upside-down like mine are in the photo):
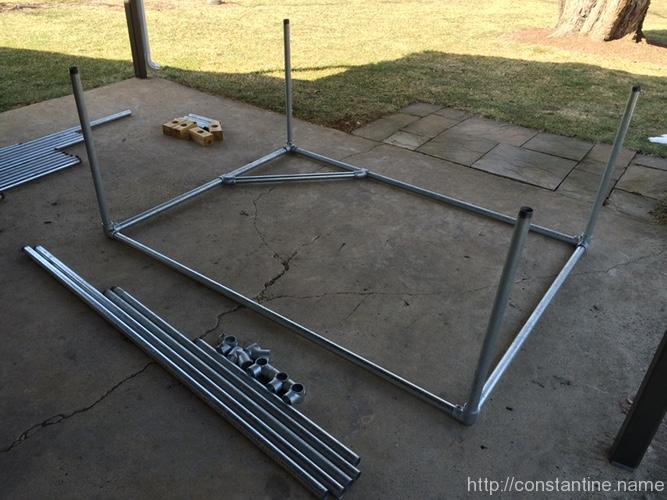
Advanced: If you’re doing the extra brace, you need to drop the second 45° angle outlet clamp onto the vertical (arrow). Later – no, do not do it now – we will install a 1-foot brace where the line is.
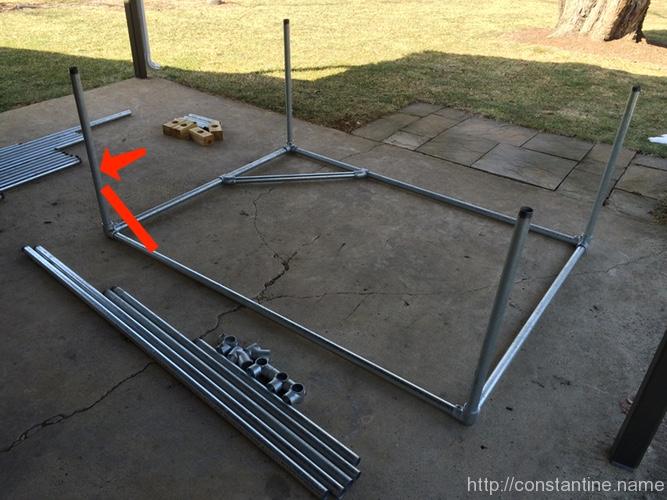
The top frame
Attach two of the 90° two outlet tees to the tops of two diagonally opposite vertical pipes. Be sure the pipes are inserted far enough so the cut off end lands correctly.
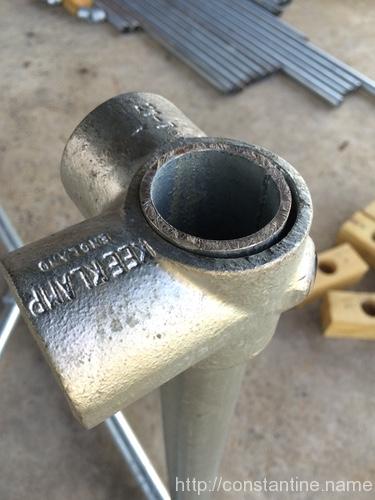
This is why the 3-foot pipes are threads-down. If the threads were currently UP, well, the threads would have to stick out. On the other hand, if you assembled this entire thing with the threads UP, when you flip it over, those threads would be PERFECT for dropping into those neat wood feet. This is how I actually set this cube up when I use it flat. I DON’T put the thread into the clamps at the very first step and then I flip the entire build over and use the wooden feet. It’s actually just like the “railings” build that we’ll do next. But I’m getting ahead of myself.
Anyway, here’s the status shot with two clamps on two of the verticals:
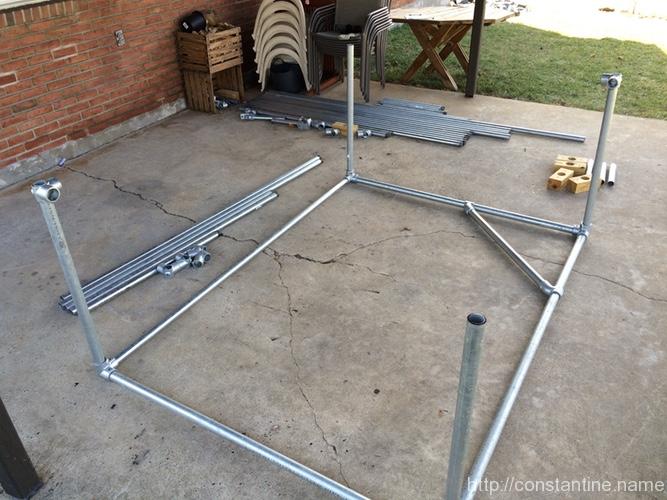
Here’s another layout shot showing the 7-foot pipe (with 45° single outlet tee) and the 5-foot pipe that will be added next. Notice I’m putting the threaded end of the 7-foot pipe down where the second diaglonal brace will go.
Advanced: The second 1-foot diagonal will go on the last 7-foot pipe, on the other side.
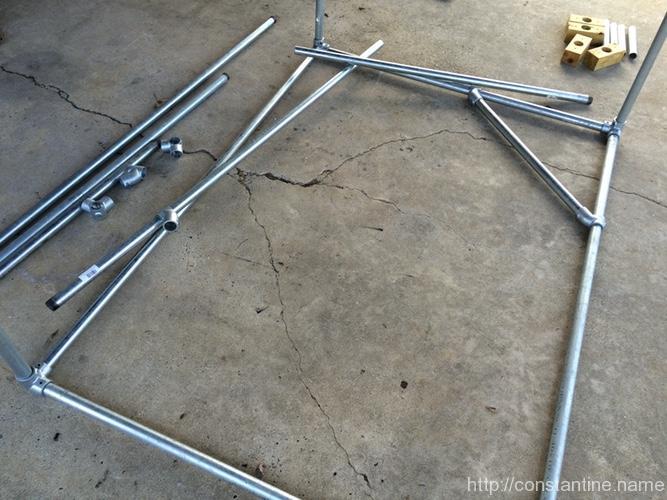
Another diatribe about safety: Loose clamps on poles lead to the “sliding death clamp” problem. You’ll experience this some day. You’ll pick up a pipe, and somewhere on the part that is NOT in your field of view, there will be a loose clamp. You’ll hear the sliding sound of a clamp… and you have a split second to figure out if the clamp is coming your way and about to pinch your fingers on the bar, or if it’s going the other way and going to hit someone else. Bonus points: if the clamp falls off, the pipe balance changes quickly and you have the slap-stick, not-funny, swinging pipe joke.
…so when you put “middle” clamps on pipes that you are going to lift or carry, snug their set screw so they don’t move.
Pickup one of the 90° two outlet tees in your right hand. (Bear with me, this is clever.) Stand inside the setup, pickup the 7-foot pipe and put the left end (with the threads) into the corner clamp:
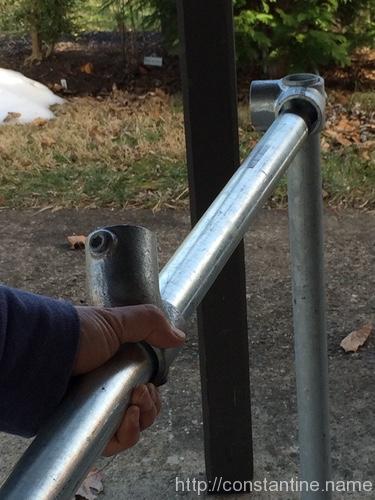
Drop the clamp onto the vertical pipe. This is not how we’ll install this clamp, I’m just using it as an extra hand. If you’re paying attention, you’ll realize this entire build can be done by yourself perfectly safely. (Nit-picking: I was also holding a camera through all of this. I should have flipped that clamp so the screws were on the other side… you’ll see in a moment.)
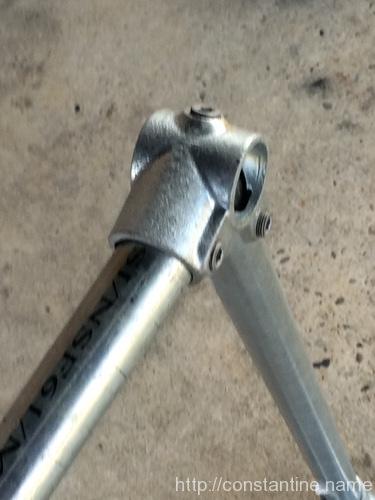
Boop! I no longer have to hold that 7-foot pipe; it’s trapped on both ends. Now go to the other end – the end we inserted first – and lock it in place with the set screw. We don’t want it coming out, and we may need to pull on it in a moment.
Next, pick up the 5-foot pipe and put the right end into the corner clamp:
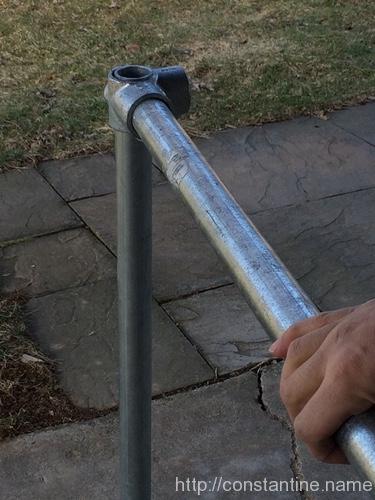
No photo for this part, but: Rest the left end on top of the 7-foot pipe, and then lock the right end of the 5-foot pipe into its corner. Like the 7-foot pipe, we may need to pull on it and we don’t want it coming out.
Now, holding the 5-foot pipe in your right hand, lift the 7-foot pipe and the clamp – and here I had to stop and flip my clamp, but you can just – rotate the clamp to receive the 5-foot pipe. (Happiness: You can’t drop either pipe because their out-of-sight ends are already locked in.)
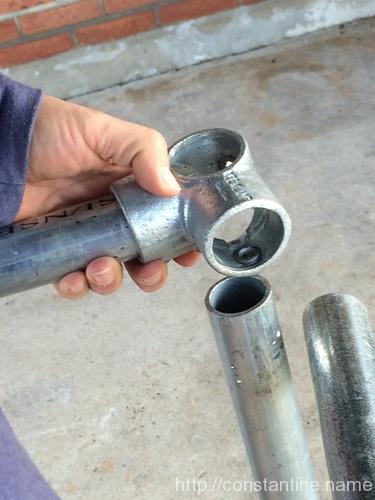
Line them up holding the clamp. Since we had the forethought to already clamp the other ends, the other ends won’t fall out on us as we wrestle this part.
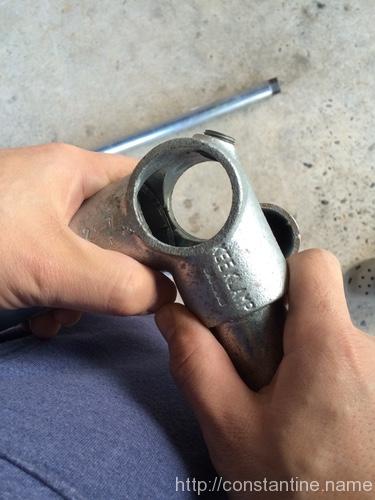
Now this gets tricky. You may have to coerce the vertical pipe to come over and want to go into this clamp. (If you’re doing the advanced version, the extra 1-foot brace would fight us at this time.) Eventually, you get this:
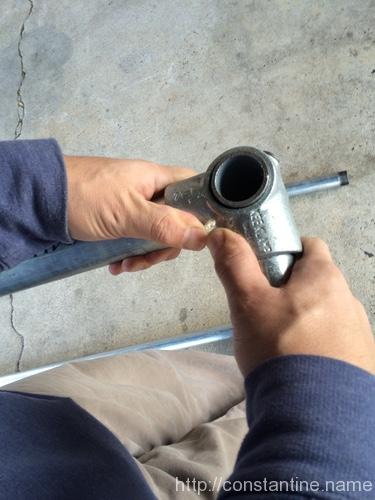
Now tighten up all three screws on this corner clamp.
Advanced: Now you can assemble and tighten the 1-foot corner brace that is on this vertical pipe.
Finally, you now have half of the upper frame:
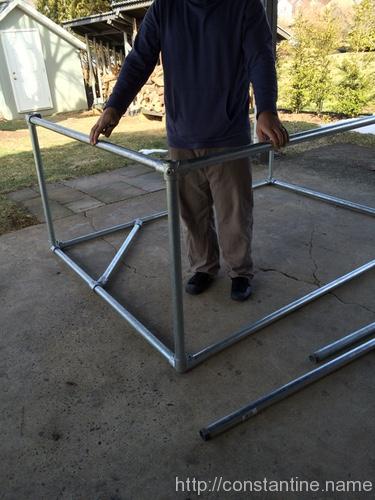
Place the last 5-foot pipe into the right side; Put the threaded end to your right (towards the braced corner.) Notice the 45° single outlet tee clamp for the top face’s corner brace is on this pipe. Use the last clamp to hold the end for you. Tighten up the far end of the 5-foot pipe. (We’re going to be pulling/pushing on this pipe like we did on the other corner.)
Advanced: If you’re doing the extra 1-foot braces with your extra 45° single outlet tees, drop the one of the 45° brackets onto the vertical pipe angled upwards.
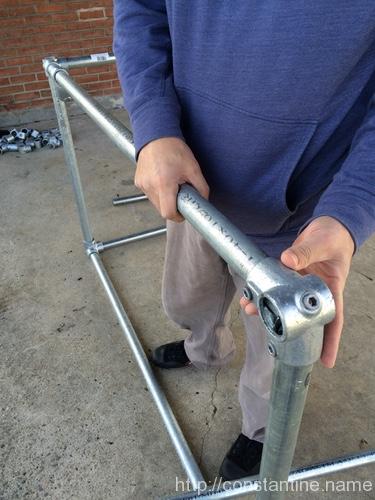
Advanced: 1-foot corner brace? Slip your last 45° single outlet onto the 7-foot pipe, angled facing the vertical.
Slip the left end (farthest away in the next photo) of the last 7-foot pipe into the far clamp. Rest the pipe on the 5-foot pipe or temporary clamp, and tighten the far end.
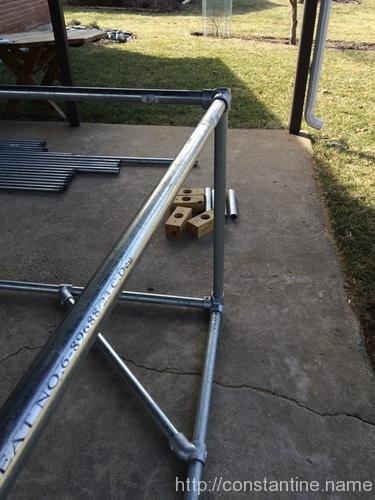
Pick up the 5-foot pipe and the clamp with your right hand, rotate the clamp to accept the 7-foot pipe:
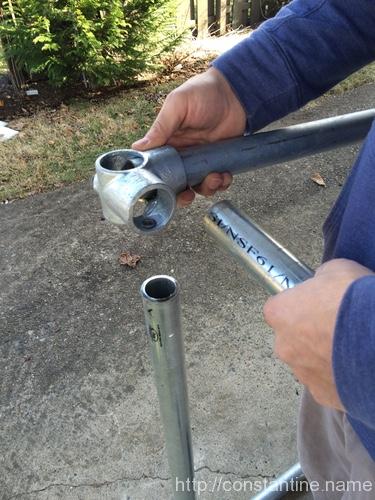
Make up the corner and coerce it into alignment:
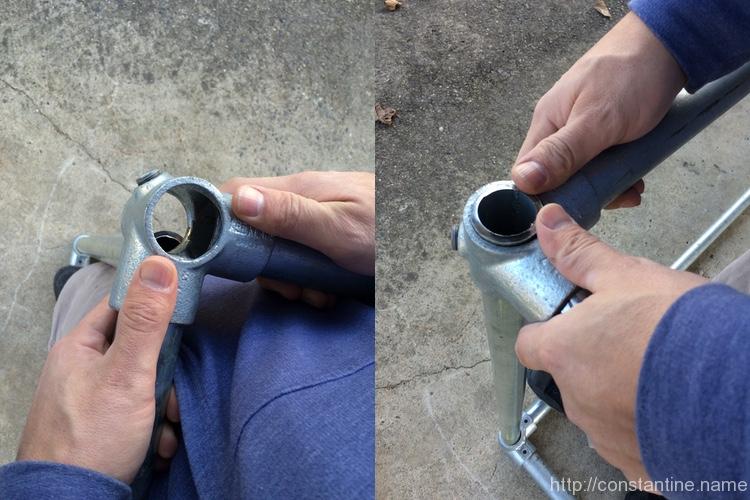
Tighten all three screws on this corner clamp.
Advanced: Make up that last 1-foot corner brace!
Finally, finish that 3-foot corner brace on the top face:
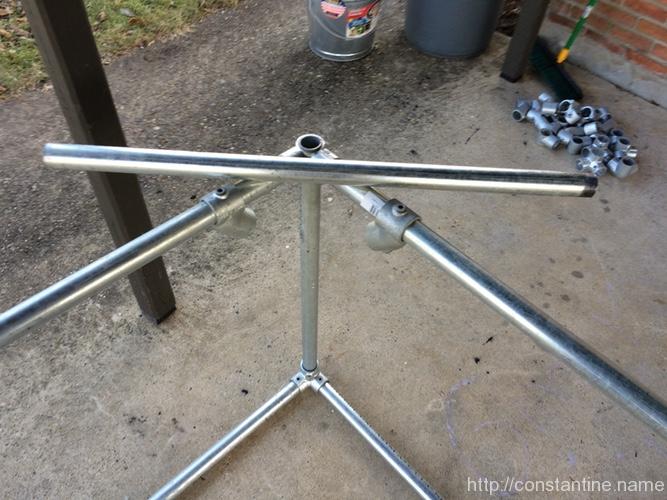
Voila!
Flat: You can use it with the round-faced outside corners down (as you assembled it), or flip the slightly more rough 90° two outlet tees to the bottom, or (bonus points) assemble threads up so they’d be sticking up at this point, then flip it over so the threads disappear inside the feet you made!
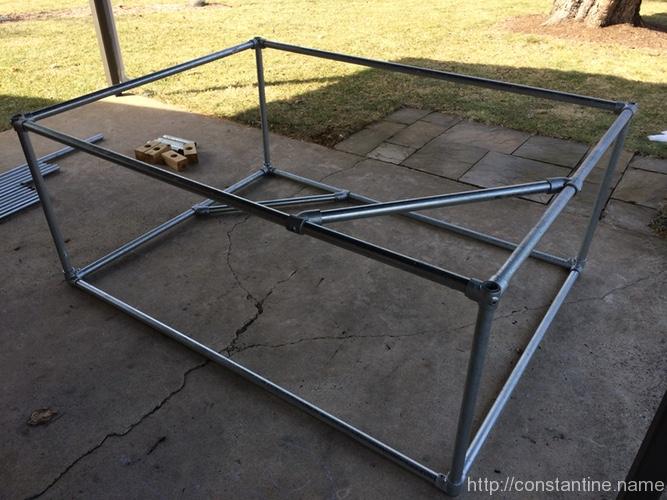
Side: Flip this way for 5-foot high climb-ups etc. You’ll learn how sturdy it is. (Answer: reasonably.)
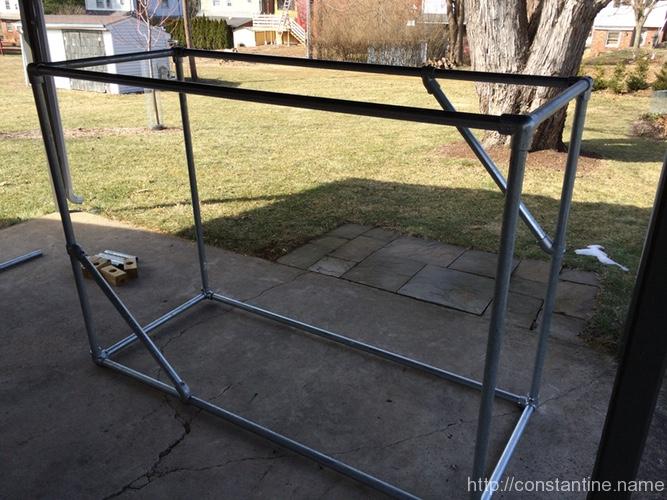
Tall: Finally, stand it up all the way for pullups or climbing challenges etc.

ɕ